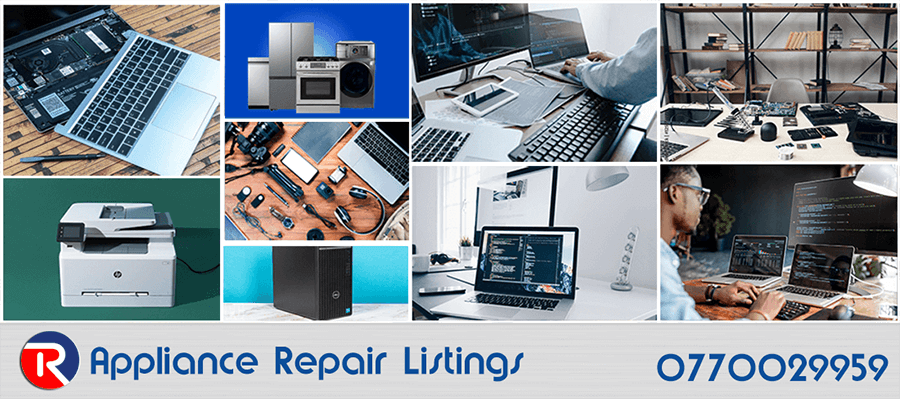
The Full Process of Elevator Setup and Installation
Elevator setup and installation is a complex, multi-stage process that requires meticulous planning, engineering expertise, and adherence to safety regulations. Elevators are critical for accessibility and efficiency in modern buildings, from residential high-rises to commercial complexes. This article provides a comprehensive overview of the entire process, detailing each phase to illustrate the precision and coordination involved.
Initial Planning and Design
The process begins with a thorough planning phase, where architects, engineers, and elevator consultants collaborate to determine the building’s requirements. Key considerations include the building’s purpose, expected passenger traffic, and space constraints. Consultants assess factors such as elevator type (passenger, freight, or service), capacity, speed, and aesthetic integration with the building’s design.
A detailed site survey is conducted to evaluate structural conditions, shaft dimensions, and electrical requirements. Engineers then select an appropriate elevator system—hydraulic, traction, or machine-room-less (MRL)—based on the building’s height and usage. Blueprints and technical specifications are drafted, ensuring compliance with local building codes and international standards, such as those set by the American Society of Mechanical Engineers (ASME) or the European Lift Directive.
"Proper planning reduces installation delays and ensures the elevator meets the building’s long-term needs." – Elevator Design Engineer
Obtaining Permits and Approvals
Before installation begins, the project must secure necessary permits from local authorities. This involves submitting detailed plans, including structural, electrical, and mechanical drawings, for review. Regulatory bodies verify compliance with safety standards, accessibility requirements (e.g., ADA in the United States), and environmental regulations. In some regions, additional approvals may be required for seismic safety or energy efficiency.
This phase can take weeks to months, depending on the jurisdiction and project complexity. Delays may occur if plans require revisions to meet code requirements. Engaging experienced consultants familiar with local regulations can streamline this process.
"Securing permits early prevents costly rework and ensures the project stays on schedule." – Building Compliance Officer
Site Preparation
Once permits are obtained, site preparation begins. This involves constructing or modifying the elevator shaft, machine room (if applicable), and pit. Contractors ensure the shaft is plumb, structurally sound, and capable of supporting the elevator’s weight and dynamic loads. The pit, located at the base of the shaft, is built to house buffers and other components, with proper drainage to prevent water accumulation.
Electrical systems are installed, including power lines for the elevator motor and control systems, as well as lighting and ventilation for the shaft and machine room. Fireproofing and sound insulation are added to meet safety and comfort standards. This phase requires close coordination between contractors, electricians, and structural engineers to avoid errors that could affect installation.
"A well-prepared site is the foundation for a safe and efficient elevator installation." – Construction Project Manager
Component Delivery and Installation
With the site ready, elevator components—such as the car, counterweights, guide rails, motor, and control systems—are delivered. These are typically manufactured off-site and shipped in modular sections to facilitate assembly. Delivery schedules are carefully planned to minimize disruption to other construction activities.
Installation begins with mounting guide rails along the shaft walls to ensure smooth movement of the elevator car and counterweight. The hoist mechanism (e.g., hydraulic piston or traction cables) is then installed, followed by the elevator car and counterweight. Electricians wire the control systems, connecting the motor, sensors, and call buttons. The car interior, including flooring, lighting, and handrails, is assembled to match the building’s aesthetic.
"Precision during component installation is critical to avoid misalignment and ensure passenger safety." – Elevator Technician
Testing and Commissioning
After installation, the elevator undergoes rigorous testing to verify performance and safety. Technicians conduct load tests, speed tests, and emergency stop tests to ensure the system operates within design specifications. Safety features, such as door sensors, brakes, and communication systems, are thoroughly checked.
Inspectors from regulatory bodies perform a final review, confirming compliance with all standards. Once approved, the elevator is commissioned for use, and operators receive training on maintenance and emergency procedures. A maintenance contract is often established to ensure long-term reliability.
"Thorough testing guarantees an elevator is safe and ready for years of service." – Safety Inspector
Ongoing Maintenance and Upgrades
Post-installation, regular maintenance is essential to keep the elevator in optimal condition. This includes lubricating moving parts, inspecting cables, and updating software for modern control systems. Over time, upgrades may be necessary to improve energy efficiency, accessibility, or aesthetics, ensuring the elevator remains functional and compliant with evolving standards.
The elevator setup and installation process, when executed with precision, results in a reliable, safe, and efficient system that enhances building functionality and user experience.