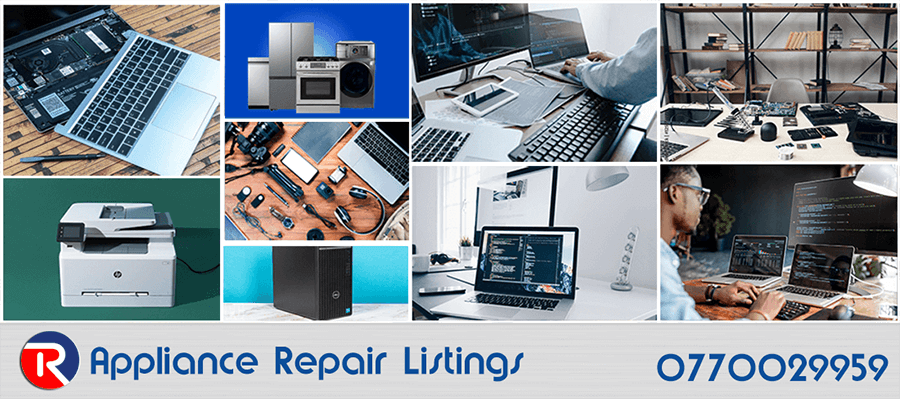
Common Postage Machine Faults, Errors, Problems, and Their Solutions
Postage machines, also known as franking machines, are essential tools for businesses that handle high volumes of mail. These devices streamline mailing processes by weighing packages, calculating postage, and printing labels. However, like any technology, postage machines can encounter faults, errors, and problems that disrupt operations. This article explores the most common issues with postage machines and provides practical solutions to ensure smooth functionality, drawing on industry-standard practices and technical support insights.
"Regular maintenance of postage machines can prevent up to 70% of common errors, saving businesses time and money." – Mailing Technology Specialist
Common Postage Machine Issues
Postage machines, such as those from Pitney Bowes and FP Mailing, are prone to specific faults that can affect performance. Below are the most frequent problems and their causes.
Poor Print Quality
Poor print quality, such as smudged, faded, or incomplete postage impressions, is a common issue. This is often caused by clogged print nozzles, low ink levels, or faulty ink cartridges. The United States Postal Service (USPS) requires clear, readable postage for mail acceptance, making this a critical problem to address promptly.
Connection Errors
Connection issues prevent the machine from communicating with the postal service’s data center for rate updates or postage refills. These errors, often indicated by codes like E010E or E1811 on Pitney Bowes machines, stem from network misconfigurations, faulty USB cables, or outdated software.
Ink Cartridge Recognition Failures
Messages like “Not Registering” or “Calibration Error” appear when the machine fails to recognize the ink cartridge. Dirty contacts, non-approved cartridges, or improper installation are typical culprits.
Paper Jams or Feeding Issues
Paper jams or improper label feeding can halt operations. These issues arise from misaligned labels, debris in the feed path, or worn rollers, particularly in high-volume machines.
Incorrect Weight Readings
Scales that display incorrect or inconsistent weights lead to inaccurate postage calculations. This can result from internal calibration errors, debris on the scale, or mechanical faults.
"Using genuine ink cartridges ensures compliance with postal regulations and reduces the risk of machine errors." – Pitney Bowes Support
Solutions to Postage Machine Problems
Addressing postage machine issues promptly minimizes downtime. Below are detailed solutions for each problem, based on manufacturer guidelines and technical support recommendations.
Resolving Poor Print Quality
To fix poor print quality:
- Run a Test Print: Most machines, like the Pitney Bowes SendPro Mailstation, allow you to print a test pattern to assess print quality. If the pattern is incomplete, proceed to cleaning.
- Clean Print Nozzles: Use the machine’s built-in cleaning function or manually clean the cartridge with a damp, lint-free cloth. For FP Postbase models, place the cartridge in hot water for 30 seconds to unclog nozzles.
- Replace Ink Cartridge: Ensure you use Royal Mail or USPS-approved cartridges. Non-approved cartridges may cause print errors or void warranties.
- Check Cartridge Installation: Remove and reinsert the cartridge, ensuring it clicks into place.
Fixing Connection Errors
To resolve connection issues:
- Check Network Settings: Verify that the machine is connected via Ethernet or Wi-Fi and that the network allows communication with the postal data center. For Pitney Bowes machines, ensure compatibility with PC Meter Connect software.
- Update Software: Download the latest version of the machine’s software (e.g., PC Meter Connect 05.00.0081). Uninstall and reinstall if necessary.
- Test USB Connections: Replug USB cables into different ports or directly into the computer, avoiding hubs. Restart the machine after reconnecting.
- Toggle Internet Settings: Adjust HTTP transfer protocol settings via the machine’s interface and test all combinations.
Addressing Ink Cartridge Recognition Failures
To fix cartridge recognition issues:
- Clean Contacts: Wipe the cartridge’s electrical contacts with a rubber eraser or alcohol wipe to remove dirt or corrosion.
- Reinstall Cartridge: Remove and firmly reinsert the cartridge until it locks into place.
- Use Approved Cartridges: Replace with manufacturer-approved cartridges to avoid compatibility issues.
- Run Maintenance Cycle: Perform a maintenance cycle through the machine’s menu to recalibrate the cartridge.
Clearing Paper Jams or Feeding Issues
To address paper jams:
- Inspect Feed Path: Power off the machine, remove any stuck labels, and clear debris from the feed path.
- Check Label Alignment: Ensure labels are loaded correctly and match the machine’s specifications.
- Clean Rollers: Wipe rollers with a damp cloth to remove dust or adhesive residue.
- Replace Worn Parts: If jams persist, contact a technician to replace worn rollers or feed mechanisms.
Correcting Incorrect Weight Readings
To fix scale issues:
- Recalibrate Scale: Access the machine’s menu to run a scale calibration. Remove all items from the scale before starting.
- Clean Scale Surface: Remove debris or dust that may interfere with weight readings.
- Test with Known Weight: Place a known weight (e.g., 1 kg) on the scale to verify accuracy.
- Contact Support: If errors persist, the scale’s internal sensors may need professional repair.
"Scheduling monthly maintenance checks can reduce postage machine downtime by up to 50%." – Mailing Equipment Technician
Preventive Measures for Postage Machines
Preventing issues is more efficient than troubleshooting. Implement these practices to maintain optimal performance:
- Use Genuine Supplies: Always use manufacturer-approved ink and labels to avoid compatibility issues.
- Perform Regular Maintenance: Clean printheads, rollers, and scales monthly. Run test prints to detect issues early.
- Update Software: Ensure the machine’s firmware and software are current to support the latest postal rates and regulations.
- Train Staff: Educate users on proper operation, including loading labels and installing cartridges, to minimize user errors.
- Schedule Professional Servicing: Arrange annual inspections by certified technicians to address wear and tear.
"A well-maintained postage machine can process up to 350 pieces per minute, even in high-volume settings." – Data-Pac Mailing Solutions
When to Seek Professional Help
While many issues can be resolved in-house, persistent problems like recurring connection errors, mechanical failures, or scale malfunctions may require professional intervention. Contact the machine’s authorized provider (e.g., Pitney Bowes, FP Mailing, or Data-Pac) for certified repairs. For USPS-related errors, such as postage statement issues (e.g., Error 5014), consult the PostalOne! Customer Care Center.
By addressing common faults promptly and adopting preventive measures, businesses can ensure their postage machines operate reliably, minimizing disruptions and maintaining compliance with postal regulations.