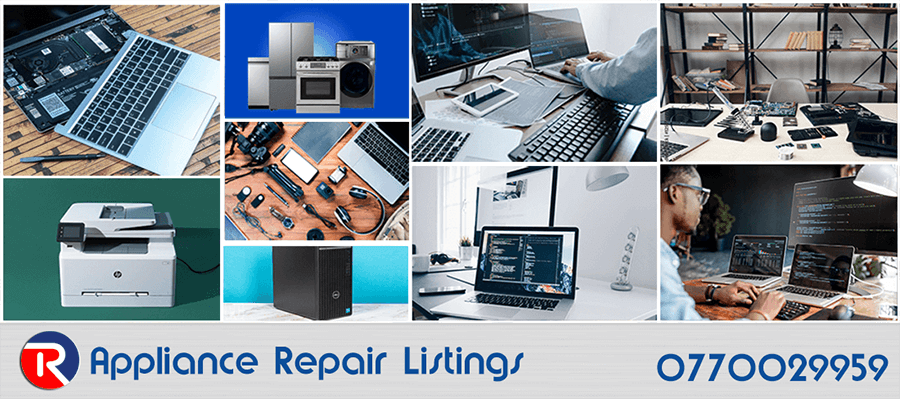
Washing Machine Lid Switch Malfunction - Reasons and How We Fix It
A washing machine lid switch malfunction can disrupt laundry routines, preventing the machine from starting or completing cycles. Repair.co.ke, a trusted appliance repair service in Kenya, specializes in diagnosing and resolving such issues efficiently. This article explores the common causes of lid switch malfunctions and outlines the professional repair process employed by Repair.co.ke to restore washing machines to optimal performance.
"A faulty lid switch is one of the most common reasons a washing machine won’t spin or agitate." – Appliance Repair Expert
Understanding the Lid Switch Function
The lid switch is a critical safety feature in top-loading washing machines, designed to ensure the machine operates only when the lid is securely closed. It prevents the drum from spinning or agitating if the lid is open, protecting users from injury. When the switch malfunctions, the machine may refuse to start, stop mid-cycle, or fail to spin, leading to incomplete washes. Recognizing the role of the lid switch is the first step in addressing its issues, and Repair.co.ke’s technicians are trained to identify related symptoms accurately.
"The lid switch acts as the machine’s safety guard, ensuring safe operation during high-speed cycles." – Repair.co.ke Technician
Common Causes of Lid Switch Malfunction
Several factors can lead to a washing machine lid switch malfunction, each requiring specific diagnostic and repair approaches. Below are the primary causes:
Physical Damage or Wear
Over time, repeated opening and closing of the lid can cause the switch mechanism to wear out or break. Physical damage, such as a cracked switch housing or bent actuator, may also occur due to forceful handling. This prevents the switch from registering the lid’s closed position.
Electrical Issues
Faulty wiring or loose connections within the switch circuit can disrupt its functionality. Corrosion or burnt contacts, often caused by moisture exposure, may also lead to electrical failures, causing the machine to misinterpret the lid’s status.
Debris or Obstruction
Lint, detergent residue, or small objects can accumulate around the switch, obstructing its movement or causing it to stick. This can falsely signal an open lid, halting the machine’s operation.
Manufacturing Defects
In rare cases, a defective switch from the manufacturer may fail prematurely, even with minimal use. Such issues are more common in specific models and may be covered under warranty.
"Regular cleaning around the lid area can prevent debris-related switch malfunctions." – Home Appliance Specialist
How Repair.co.ke Diagnoses the Issue
Repair.co.ke employs a systematic approach to diagnose washing machine lid switch malfunctions. The process begins with a thorough inspection of the machine, focusing on the lid switch assembly. Technicians use multimeters to test the switch’s continuity, confirming whether it correctly signals the lid’s status. They also check for visible damage, debris, or wiring issues.
To ensure accuracy, Repair.co.ke’s team reviews the machine’s error codes (if available) and tests other components, such as the control board, to rule out related problems. This comprehensive diagnosis pinpoint’s the root cause, enabling targeted repairs.
"Precise diagnostics save time and ensure the right fix is applied the first time." – Repair.co.ke Service Manager
Repair.co.ke’s Repair Process
Once the issue is identified, Repair.co.ke follows a structured repair process to address the lid switch malfunction:
Cleaning and Maintenance
For debris-related issues, technicians clean the switch area, removing lint or obstructions. They lubricate moving parts if necessary to restore smooth operation.
Switch Replacement
If the switch is damaged or electrically faulty, Repair.co.ke replaces it with a compatible, high-quality part. Technicians ensure proper alignment and secure connections to prevent future issues.
Wiring Repairs
For electrical problems, the team repairs or replaces damaged wires and connectors, sealing them against moisture to enhance durability.
Testing and Calibration
After repairs, the machine is tested through multiple cycles to confirm the switch functions correctly. Technicians verify that the machine starts, agitates, and spins as expected.
Repair.co.ke sources parts from reputable suppliers, ensuring compatibility with various washing machine brands and models. Their repairs are backed by a service warranty, providing peace of mind for clients.
"Using genuine parts during repairs extends the lifespan of your washing machine." – Appliance Repair Consultant
Preventing Future Malfunctions
To minimize the risk of lid switch issues, Repair.co.ke advises regular maintenance, such as cleaning the lid area and avoiding forceful lid handling. Users should also inspect the machine for unusual noises or error codes and address them promptly. Scheduling periodic professional check-ups can catch potential problems early, ensuring long-term reliability.
"Proactive maintenance can prevent 80% of common washing machine issues." – Repair.co.ke Support Team
Why Choose Repair.co.ke?
Repair.co.ke stands out for its expertise, prompt service, and commitment to customer satisfaction. Their skilled technicians handle lid switch malfunctions with precision, restoring washing machines to full functionality. Whether it’s a minor fix or a complex repair, Repair.co.ke delivers reliable solutions tailored to each client’s needs.
Contact Information
For professional washing machine repairs, contact Repair.co.ke:
- Website: repair.co.ke
- Email: info@repair.co.ke